Способ приготовления предшественника катализатора для синтеза Фишера-Тропша, который предусматривает на начальной стадии обработки проведение обработки суспензии, которая содержит подложку катализатора, предшественник активного компонента катализатора и воду, при повышенной температуре T1 и под давлением P1 ниже атмосферного, таким образом, чтобы осуществить пропитку подложки предшественником активного компонента катализатора и частичную сушку пропитанной подложки или носителя. Температура T1 поддерживается в диапазоне 60oC≤T1≤95oC и под давлением P1 ниже атмосферного в диапазоне от атмосферного до вакуума 20 кПа(а) при T1=60oC и в диапазоне от атмосферного до вакуума в 83 кПа(а) при T1=95oC. Начальную стадию обработки не продолжают далее точки, в которой пропитанная подложка имеет потери при прокаливании ('LOI'), которые составляют менее 1,2 потерь при прокаливании при исходной влажности ('LOIiw'). На последующей стадии обработки проводят обработку частично высушенной пропитанной подложки при повышенной температуре Т2 и под давлением Р2 ниже атмосферного таким образом, чтобы получить высушенную пропитанную подложку, которую прокаливают для получения предшественника катализатора. Температура Т2 и давление ниже атмосферного P2 поддерживаются таким образом, что 60oC<Т2≤95oC и T2>T1 и/или Р2<20 кПа(а) и P2<P1. Предшественник катализатора восстанавливают для получения катализатора. Способ также предусматривает хранение высушенного пропитанного носителя или подложки после последующей стадии обработки в сухих условиях при температуре окружающей среды, перед прокаливанием указанного материала, причем допустимое время хранения должно быть меньше чем ((-8,1/LOIiw)LOIunload+26,2) ч, где LOIunload представляет собой потери LOI, при которых была закончена последующая стадия обработки. Великолепные свойства катализатора, полученные в ходе сушки, сохраняются до момента его прокаливания. В соответствии с изобретением предлагается оптимизация процедуры сушки при приготовлении предшественника катализатора, из которого может быть получен катализатор с великолепными характеристиками синтеза Фишера-Тропша, обладающий высокой активностью. Более конкретно, в соответствии с изобретением предлагается эффективная сушка пропитанного материала в ходе приготовления предшественника катализатора, причем великолепные свойства катализатора, полученные в ходе сушки, сохраняются до момента его прокаливания. 26 з.п. ф-лы, 7 табл., 6 ил.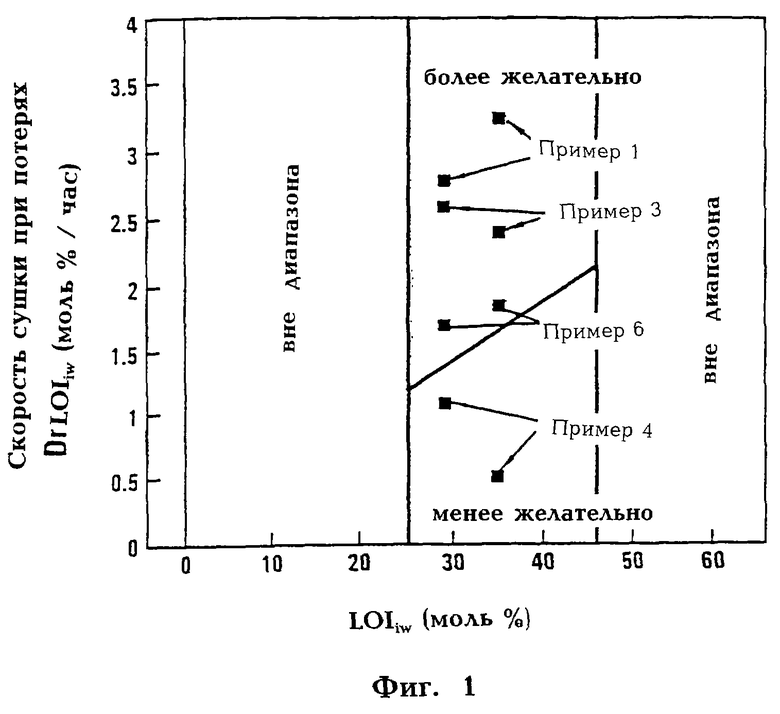
1. Способ приготовления предшественника катализатора Фишера-Тропша, отличающийся тем, что он предусматривает на начальной стадии обработки проведение обработки суспензии, которая содержит пористую оксидную подложку или носитель катализатора, активный компонент катализатора или его предшественник, а также воду, при температуре T1 в диапазоне 60°C ≤ T1 ≤ 95°C и под давлением P1 ниже атмосферного в диапазоне от атмосферного до вакуума 20 кПа(а) при T1=60°C и в диапазоне от атмосферного до вакуума 83 кПа(а) при T1=95°C таким образом, что происходит пропитка подложки или носителя активным компонентом катализатора или его предшественником и частичная сушка пропитанной подложки или носителя, причем начальную стадию обработки не продолжают далее точки, в которой пропитанная подложка или носитель имеет потери при прокаливании ('LOI'), которые составляют менее 1,2 потерь при прокаливании при исходной влажности ('LOIiw'); после чего на последующей стадии обработки проведение обработки частично высушенной пропитанной подложки или носителя при повышенной температуре Т2 и под давлением ниже атмосферного P2 таким образом, что 60°С < Т2 ≤ 95°С и T2 > T1 и/или Р2 < 20 кПа(а) и Р2 < Р1, в результате чего достигают более сильной сушки пропитанной подложки или носителя на последующей стадии обработки, чем на начальной стадии обработки, и получают высушенную пропитанную подложку или носитель; и прокаливание высушенной пропитанной подложки или носителя с получением предшественника катализатора.2. Способ по п.1, отличающийся тем, что пористая оксидная подложка катализатора представляет собой порошок оксида алюминия и имеет средний диаметр пор от 8 до 50 нм, причем объем пор подложки составляет от 0,1 до 1 мл/г, а средний размер частиц составляет от 1 до 500 мкм, при этом в качестве активного компонента предшественника катализатора используют нитрат кобальта (Со(NO3)2·6Н2O).3. Способ по п.2, отличающийся тем, что на начальной стадии обработки используют от 1,18ху до 1,82ху кг нитрата кобальта (Со(NО3)2·6Н2O), где х представляет собой BET объем пор подложки из оксида алюминия (мл/г), а у представляет собой массу пропитываемой подложки из оксида алюминия (кг).4. Способ по п.3, отличающийся тем, что производят первоначальное растворение нитрата кобальта (Со(NО3)2·6Н2O) в воде, причем используют количество воды, достаточное для того, чтобы объем раствора превышал ху литров; нагревание раствора до 60-95°С; добавление в раствор материала подложки при атмосферном давлении, в результате чего получают суспензию, причем производят непрерывное перемешивание суспензии.5. Способ по одному из пп.2-4, отличающийся тем, что при проведении начальной стадии обработки к суспензии постепенно прикладывают вакуум при ее непрерывном перемешивании при температуре Т в диапазоне 60°C ≤ T1 ≤ 95°C и давлении P1, которое лежит в диапазоне от атмосферного до Р1 ≥ 20 кПа(а).6. Способ по п.5, отличающийся тем, что начальную стадию обработки продолжают до точки, в которой пропитанная подложка из оксида алюминия имеет потери при прокаливании ('LOI'), которые составляют 1,2 потерь при прокаливании при исходной влажности ('LOIiw').7. Способ по п.6, отличающийся тем, что при потере LOI пропитанной подложки из оксида алюминия, равной 1,2 LOIiw, применяют интенсивное снижение давления на последующей стадии обработки таким образом, что Р2 < Р1, причем одновременно поддерживают температуру подложки в диапазоне от 60-95°С при непрерывном перемешивании, так что имеет место более интенсивная сушка пропитанной подложки в ходе последующей стадии обработки.8. Способ по п.7, отличающийся тем, что без перерыва приступают к более интенсивной вакуумной сушке в ходе последующей стадии обработки, которую проводят при минимальном достижимом давлении Р2, причем вакуумную сушку при указанных условиях продолжают до достижения определенного максимума требуемой величины LOI, причем этот максимум требуемой величины LOI равен 0,90 LOIiw или меньше этого значения.9. Способ по п.7 или 8, отличающийся тем, что в ходе последующей стадии обработки контролируют скорость сушки суспензии путем управления уровнем давления ниже атмосферного Р2 за счет установки степени перемешивания или управления ею, за счет установки температуры обработки Т2 или управления ею и/или за счет введения горячего воздуха в суспензию.10. Способ по п.9, отличающийся тем, что в ходе последующей стадии обработки контролируют скорость сушки таким образом, что в точке исходной влажности скорость сушки превышает значение (0,048 ч-1) LOIiw.11. Способ по п.9 или 10, отличающийся тем, что он предусматривает хранение высушенного пропитанного носителя или подложки после последующей стадии обработки в сухих условиях при температуре окружающей среды перед прокаливанием указанного материала, причем допустимое время хранения должно быть меньше ((-8,1/LOIiw)LOIunload+26,2) ч, где LOIunload представляет собой потери LOI, при которых была закончена последующая стадия обработки.12. Способ по одному из пп.2-11, отличающийся тем, что прокаливание высушенной пропитанной подложки осуществляют в кальцинаторе с псевдоожиженным слоем или во вращающейся обжиговой печи при 200-300°С.13. Способ по одному из пп.2-12, отличающийся тем, что используют первоначальное количество нитрата кобальта, достаточное для получения содержания кобальта в диапазоне от 5 до 70 г Со на 100 г подложки.14. Способ по одному из пп.2-13, отличающийся тем, что для получения увеличенного содержания кобальта в подложке из оксида алюминия прокаленный материал подвергают дополнительной пропитке, сушке и прокаливанию в ходе второй операции пропитки, причем начальная стадия обработки, последующая стадия обработки и прокаливание образуют первую операцию пропитки.15. Способ по п.14, отличающийся тем, что вторая операция пропитки предусматривает на начальной стадии обработки проведение обработки суспензии, которая содержит прокаленный материал после первой операции пропитки, кобальт в качестве активного компонента катализатора или его предшественника, а также воду при повышенной температуре T1' в диапазоне 60°C ≤ T1 ≤ 95°C и под давлением ниже атмосферного P1' в диапазоне от атмосферного до вакуума 20 кПа(а) при T1'=60°C и в диапазоне от атмосферного до вакуума в 83 кПа(а) при T1'=95°C таким образом, что происходит пропитка прокаленного материала активным компонентом катализатора или его предшественником и частичная сушка пропитанного материала, причем начальную стадию обработки не продолжают далее точки, в которой пропитанный материал имеет потери при прокаливании ('LОI'), которые составляют менее 1,2 потерь при прокаливании при исходной влажности ('LOIiw'); после чего на последующей стадии обработки проведение обработки частично высушенного пропитанного материала при температуре Т2' и под давлением ниже атмосферного P2' таким образом, что 60°C<T2'≤95°C и T2'>T1' и/или Р2'<20 кПа(а) и P2'<P1', в результате чего достигают более сильной сушки пропитанного материала на последующей стадии обработки, чем на начальной стадии обработки, и получают высушенный пропитанный материал, и прокаливание высушенного пропитанного материала с получением предшественника катализатора.16. Способ по п.15, отличающийся тем, что при проведении второй операции пропитки используют нитрат кобальта (Со(NО3)2·6Н2O) в качестве активного компонента предшественника катализатора, причем количество используемого на начальной стадии обработки второй операции пропитки нитрата кобальта лежит в диапазоне от 1,18x1y1 до 1,82x1y1 (кг) (Со(NО3)2·6Н2O), где x1 представляет собой BET объем пор прокаленного материала после первой операции пропитки (мл/г), a y1 равен массе (кг) прокаленного материала после первой операции пропитки, который должен быть пропитан в ходе второй операции пропитки, при условии, что регулируют количество нитрата кобальта (Со(NО3)2·6Н2O), используемого в ходе второй операции пропитки, если максимальное количество (Со(NО3)2·6Н2O), определенное по формуле 1,82x1y1, приводит к превышению желательного содержания кобальта в предшественнике катализатора.17. Способ по п.16, отличающийся тем, что он предусматривает в ходе второй операции пропитки первоначальное растворение нитрата кобальта (Со(NО3)2·6Н2O) в воде с использованием количества воды, достаточного для получения объема раствора более x1y1 литров; нагрев раствора до 60-95°С; добавление в этот раствор при атмосферном давлении конечного запаса y1 кг прокаленного материала, полученного от первой операции пропитки, для образования суспензии и непрерывное перемешивание суспензии.18. Способ по п.16 или 17, отличающийся тем, что при проведении начальной стадии обработки второй операции пропитки к суспензии постепенно прикладывают вакуум при ее непрерывном перемешивании при температуре T1' в диапазоне 60°C≤T1'≤95°C и под давлением P1' в диапазоне от атмосферного до Р1'≤20 кПа(а).19. Способ по п.18, отличающийся тем, что начальную стадию обработки второй операции пропитки продолжают до точки, в которой пропитанный материал имеет потери при прокаливании ('LOI'), которые составляют 1,2 потерь при прокаливании при исходной влажности ('LOIiw').20. Способ по п.19, отличающийся тем, что, когда потери LOI пропитанного материала становятся равными 1,2 LOIiw, применяют интенсивное снижение давления на последующей стадии обработки второй операции пропитки таким образом, что P2'<P1', причем одновременно поддерживают температуру частично высушенного пропитанного материала в диапазоне 60-95°С при непрерывном перемешивании, при этом происходит более интенсивная сушка пропитанного материала в ходе последующей стадии обработки.21. Способ по п.20, отличающийся тем, что без перерыва приступают к более интенсивной вакуумной сушке в ходе последующей стадии обработки, которую проводят при минимальном достижимом давлении, причем вакуумную сушку при указанных условиях продолжают до достижения четко определенного максимума требуемой величины LOI, при этом указанный максимум требуемой величины LOI равен 0,90 LOIiw или меньше этого значения.22. Способ по п.20 или 21, отличающийся тем, что в ходе последующей стадии обработки контролируют скорость сушки суспензии путем управления уровнем давления ниже атмосферного P2' за счет установки степени перемешивания или управления ею, за счет установки температуры обработки T2' или управления ею и/или за счет введения горячего воздуха в суспензию.23. Способ по п.22, отличающийся тем, что в ходе последующей стадии обработки контролируют скорость сушки таким образом, что в точке исходной влажности скорость сушки превышает значение (0,048 ч-1) LOIiw.24. Способ по п.22 или 23, отличающийся тем, что он предусматривает хранение высушенного пропитанного носителя или подложки после последующей стадии обработки в сухих условиях при температуре окружающей среды перед прокаливанием указанного материала, причем допустимое время хранения должно быть меньше чем ((-8,1/LOIiw)LOIunload+26,2) ч, где потери LOIunload представляют собой потери LOI, при которых была закончена последующая стадия обработки.25. Способ по одному из пп.16-24, отличающийся тем, что прокаливание высушенного пропитанного материала осуществляют в кальцинаторе с псевдоожиженным слоем или во вращающейся обжиговой печи при 200-300°С.26. Способ по одному из пп.2-25, отличающийся тем, что ходе первой стадии обработки первой операции пропитки и/или в ходе первой стадии обработки второй операции пропитки добавляют в виде предшественника растворимую в воде соль палладия (Pd) или платины (Pt), которая действует в качестве примеси, способной усиливать восстановимость активного компонента, причем пропорция по массе металлического палладия или платины к металлическому кобальту составляет от 0,01:100 до 0,3:100.27. Способ по п.2, отличающийся тем, что в ходе начальной стадии обработки используют от 1,18ху до 1,82ху кг нитрата кобальта (Со(NО3)2·6Н2O), где х представляет собой BET объем пор подложки из оксида алюминия (мл/г), а у представляет собой массу пропитываемой подложки из оксида алюминия (кг), причем производят первоначальное растворение (Со(NО3)2·6Н2O) в воде, при этом используют достаточное количество воды для того, чтобы объем раствора превышал ху литров; добавление в раствор материала подложки при температуре окружающей среды, в результате чего получают суспензию; после этого нагревание суспензии до повышенной температуры в диапазоне 60-95°С, причем давление ниже атмосферного или вакуум, которые прикладывают в ходе начальной стадии обработки, доводят до 20 кПа(а).