I
Изобретение относится к металлургии чугуна, в частности к способам изготовления отливок из чугуна с шаровищоым графитом, обладающих повышенньгм сопротивлением хрупкому разрушению.
Известны способы изготовления отливок из нелегированных чугуиов с шароввдным графитом, включающим расплавление шихтовых: материалов, перегрев, сфероидизирующую и графитизирующую обработку, заливку форм и термообработку, как правило, двухстадийную. Эти способы обеспечивают получение высокого относительного удлинения (cf ) и ударной вязко,сти (su ), необходимых для применения в условиях работы под давлением корпусных деталей энергетического и др. оборудования, и направлены на получение гомогенной ферритрой структуры металлической основы ш.
Наиболее близким по технической сущности и достигаемой цели является способ изготовления отливок из чугуна с шаровидным графитом и способ их термообработки, состоящий из выбора и подготовки шихтовых материалов с низким содержанием фосфора (менее 0,12%) и марганца (менее 0,6%), расплавления шихтовых материалов и перегрева расплава, обработки расплава сфероидизируюшими присадками на основе магния и его сплавов, обработки расплава графитизирующими модификаторами, как правило, совместно с флюсами, и удаления шлака, разливки металла по формаМд кристаллизации и охлаждения отливок J2J. ,
Термообработка состоит из двух стадий и включает:
1.Двухступенчатый отжиг в стационарном тепловом поле для разложения оементита и ферритизааин металлической основы 1ФИ температурах Ао+1С/Ь и соответственно. Время выдержки .ют дрстаточньш one завершевкя оботос гцюцессов - 2-6 ч.2.Низкотемпературный отжИг в ста, ционарном тепловом поле для Снятия }цш ряжений в сложных деталях, приъ еняемый как после выбивки, так и охлаждения на воздухе после термообработки, Недостатком известных способов изготовления стали из чугуна с шаровидным графитом является то, что, несмотря на высокий уровень относительного удлинения, основной показатель механики линейного разрушения Ь чугуна остается низким и не превышает 1ОО кгс/мм. При этом Kjjj слабо зависит от неправильности ишровидной формы графита, структуры металлической основы и механических свойств. Вместе с тем эта характеристика является главной при определении эксплуатационной надежности и долговечности работы детали, так как она характеризует ее работоспособность при наличии дефектов (раковин, трещин и др.), скорость их роста и допустимые размеры. Цель изобруетения - повышение сопротивления хрупкому разрушению. Цель достигается тем, что согласно способу отливок из чугуна с шаровидным графитом, заключаюшийся в расплавления шихтовых материалов содержащих О,ОО5- О,05% фосфора, перегрев расплава, вводе сфероидизаторов и графитизаторов в ковш при выпуске в него расплава, залив ке форм, в расплав перед выпуском из печи вводят легирующие аустенитообразую ише элементы, при выпуске в ковш перед вводом сфероидизаторов раскисляют силикокальцием 0,5-1,5% от веса металла и алюминием 1,0-1,5 суммы содержания хрома и молибдена в чугуне, при этом расплав ремодифицируют периевыми РЗМ. В качестве аустенитообразующкх легИ рующих элементов в расплав вводят Hi , Си . Мо, С( , в следующем количестве, в % от веса расплава: 0,5-2,0 Ni Си 0,3-1,5 МоО.О5-О.15 ,03-О,40 Цериевые РЗМ вводят в количестве О,ОЗ-О,О5% от веса расплава. Кроме того, согласно способу термообработки отливок из чугуна с шаровидны графитом, включающему графитизируюпщй отжиг при теш1ературе в течеяие 2-4 ч и ферритизирующий отжиг при температуре в течение 3-6 ч, после ферритизируюшего отжига проводят дополнительный нагрев со скоростью 2- 5 град/мин до температуры С, выдерживают при этой температуре в течение 0,2-2 ч, охлаждают на воздухе до температуры - (1О-2О С), а затем охлажлакгг со скоростью ЗО-60О гр)ая/м Дополнительный нагрев ведут от 1 до раз. Для деталей сложной конфигурации доолнительно проводят отпуск в течение -6 ч при 2 80-300 С. Легирование чугуна аустенитообразуюими элементами в указанных количестах производят для понижения устойчивоси феррита при термообработке и облегчеии выделения новой фазы при рекристализационной термообработке. Увеличение оличества легирующих элементов выше указанных пределов способствует образованию бейнито-перлитных структур и снижению сопротивления хрупкому разрушению. Раскисление расплава чугуна при выпуске в ковш силикокальцием в количестве О,5-1,5% способствует удалению из расплава кислорода и серы, увеличению продолжительности сфероидизирующего эффекта, измельчению графита и перераспределению фосфора в структуре чугуна. Введение силикокальпия в количестве, меньшем 0,5%, не обеспечивает получе-. ния указанных эффектов, а количество, большее 1,5% способствует насыщению чугуна кремнием и затрудняет процесс получения качественных деталей. Введение в расплав при выпуске в ковш алюминия в количестве 1,0-1,5 суммы содержания хрома и молибдена препятствует образованию цементита, снижает его устойчивость при отжиге, способствуя переходу этих элементов в твердый раствор, снижая тем самым его устойчивость при последующем рекристаллизационном отжиге, и способствуя выделению новой фазы, обогащенной хромом и молибденом. Большие присадки алюминия приводят к образованию литейных дефектов, меньшие не обеспечивают, при наличии в чугуне хрома, полной графитизации в процессе кристаллизации и отжига. Ремодифиаироваиие аериевыми РЗМ необходимо для нейтрализации охрупчнвающего влияния на феррит микрохфимвсей поверхностно-активных цветных металлов: мышь5Ша, висмута, сурьмы и др. и стабилизации сфероидизирующего действия магния. Присадки РЗМ в больших количествах .дриводят к затруднению графитнзации в процессе кристаллизации и термообработки, а в менышос необеспечивают нейтрализацию вредных примесей. В способе термообработки температура нагрева, продолжительность выдержки, скорость нагрева и охлаждения, как и число нагревов и охлаждений, зависят от состава чугуна и устанавливаются но дилатометрическим кривым нагрева и охлаждения, а также в зависимости от мас сы и конструкции деталей. Отклонение от указанных температурных, временных и скоростных рюжимов термообработки приводит к появлению пе лито-мартенситных структур или не обеспечивает выпадение новой фазы, что в обоих случаях приводит к снижению сопротивления хрупкому разрушению. При охлаждении сложных разностенны деталей при быстром охлаждении тонких частей возможно получение больших остаточных напряжений, для снятия которы целесообразно проводить низкотемператур ный отпуск при 280-3 . При реализапии способа плавку проводили в печи ИЧТ на шихтовых материалах, состоящих из ПВК-3, содержащими 0,14% Р и 0,11% MVi , и стальной высе ки. После расплавления чугуна в печь при садили 1,3% N-i, 0,6% Си и О,1% Мо. Со держание хрома определялось присутствием его в шихтовых материалах. При выпуске из печи металл обрабатывали 0,8% Са 5i , 0,3% АК , что составляло величину, в 1,5 раза превышаю щую сумму содержания Су и Мо в чугуне, и 0,03% мишметалла. После удаления шлака расплав модифицировали магнием в количестве 0,25%, затем модифицировали вторично Fe5i в количестве 0,5% и .разливалиПО формам. Отлитые заготовки термообрабатывали по режиму: нагрев в течение 5 ч до , выдержка 4 ч, схклаждение с печью до 75О С, вьщержка 4 ч и охлаждение с печью, далее трехкратная рекристаллизационная термообработка по режиму: нагрев с печью до 75О С, выдержка 1 ч, охлаждение на воздухе до 650 С и последующее охлаждение со скоростью 60 град/мин Исследование структуры и свойств полученного чугуна с ша ювидньгел графитом состава,%:СЗ,08; Si 2,2; Ми 0;25ГР 0,007;вО,ООЗГр. О,1О;); Нл 1,3;Ох 0,6;Мо О, О,15,15, показало, что , не сягЛЙаясь по езс(йическим свойствам ( ЗЪ , Ja , , НВ) от обычного ферритового чугуна, полученного обычным способом, он характеризуется в 1,5 раза более дисперсными включениями графита, особым строением межзеренных границ, при этом в составе фаз выделяющихся по границам зерен, наблюдается повышенное на 2О% содержание аустенитообразующнх элементов (,, О, Си , Мо) и на 2О% меньшее содержание крегдния, в сравнении с основной металлической матрицей - гЬерритом. В результате указанных изменений в структуре в 1О раз уменьшилась скорость роста трещины, приблизив чугун по этому показателю в кованой роторной стали 25ХНЗМФА. Коэффициент интенсивности напряжений, характеризующий сопротивление распространению трещин, BO3fэс в 3,5-4 раза,, достигнув 350 кгс/мм . Ожидаемый экономический эффект226 т.руб. в год. Формула изобретения 1. Способ изготовления отливок из чугуна с шаровидным графитом, заключающийся в расплавлении шихтовых материалов содержащих О,ОО5-О,О5% фосфора, перегреве расплава, вводе сфероидизаторов и графитизаторов в ковш при выпуске в него расплава и заливке форм, о тличающийся тем, что, с целью повышения сопротивления хрупкому разрушению, в равплав перед выпуском из печи вводят легирующие аустенитообразующие элементы, при выпуске в ковш перед вводом сфероидизаторов раскисляют силикокальцием 0,5-1,5% от веса металла и алюминием 1,О-1,5 суммы содержания хрома и молибдена в чугуне, при этом расплав ремодифицируют первыми РЗМ. 2.Способ по п. 1, отличающий с я тем, что в качестве аустенито образующих элементов в расплав вводят никель, медь, молибден и хром в следующем количестве, в % от веса расплава: Никель0,5-2,0 МедьО,3-1,5 Молибден0,05-0,15 Хром0,ОЗ-О,4О 3.Способ по п. 1, отличаюий с я тем, что цериевые РЗМ ввоят в количестве 0,ОЗ-О,О5% от веса асплава. 4.Способ термообработкиотливок иэ угуна с шаровидным графитом, включащий графитизирующий отжиг при темпеатуре Acu+lcPc в течение 2-4 ч и феритизирукшшй отжиг при температуре О +10РС в течение 3-6 часов отичающийся тем, что, с целью овышения сопротивления хрупкому раэру ению, после ферритизируюшего отжига роводят дополнительный напрев со скоостью 2-5 град/мин до температуры.7 8659178
ACjtlO C, выдерживают при этой темпе-Источники информации,
ратуре в течение 0,2-2 ч, охлаждают напринятые во внимание при экспертизе воздухе до температуры Ah (1О-2СГС),
а затем охлаждают со скоростью ЗО-1. Ващенко К. И., Софрони Л. Магни600 град/мин.5 евый чугун. Машгиз, 1960, с. 2О7-21О.
5. Способ по п. 4, о т л и ч а ю -2. Цьшин И. О, Высокопрочный чущ и и с я тем, что дополнительный на1 -гун с шаровидным графитом. М., 1958,рев ведут от 1 до 5 раз.с. 51.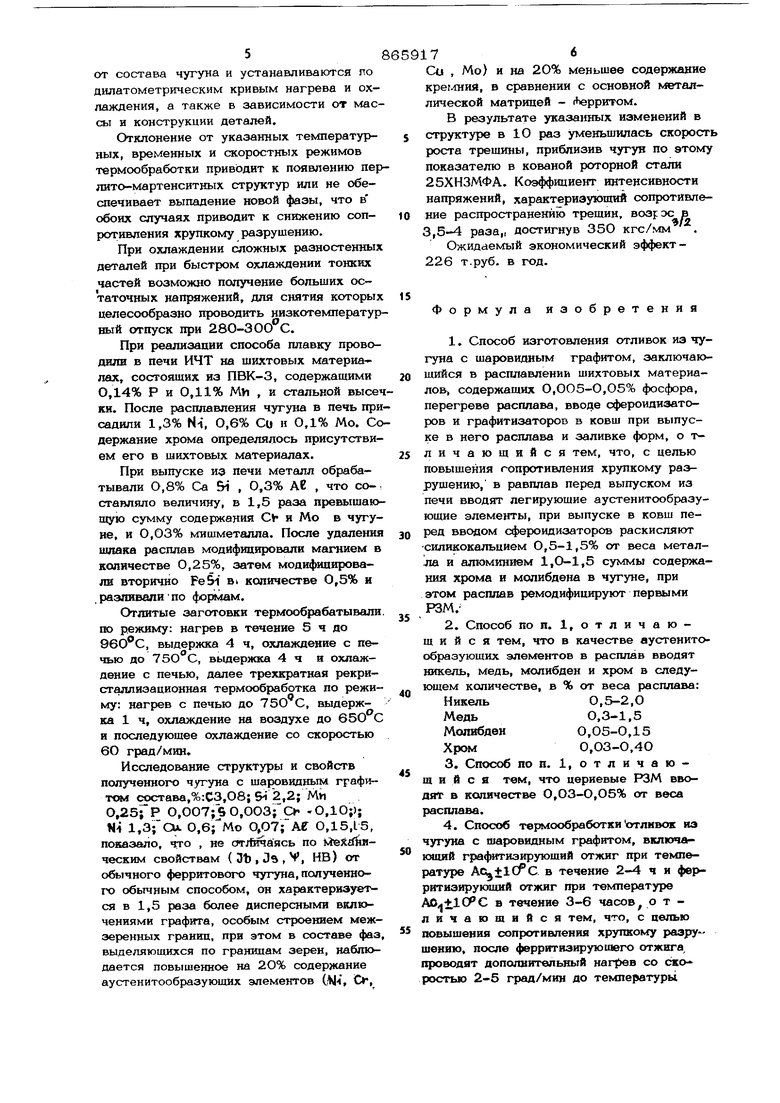